Etched-foil heaters have gained significant popularity due to their flexibility, uniform heat distribution, and rapid response times. These heaters consist of a resistive heating element etched onto a thin foil substrate, providing excellent thermal conductivity. Accurate estimation of power requirements is essential for designing the electrical circuitry and ensuring optimal performance of the heating system.
This calculator models the conduction, radiation, and convection losses of a heat sink, as well as process heat requirements, to assist you in determining heater wattage needs. Add input values in the appropriate fields below and the calculator will provide an estimate the minimum heater wattage. See the “Minco Heater Wattage Estimator” video for further instruction.
For more detail on estimating heater wattage, see our corresponding white paper, “Estimating Power Requirements of Etched-Foil Heaters“.
Thermal System Example
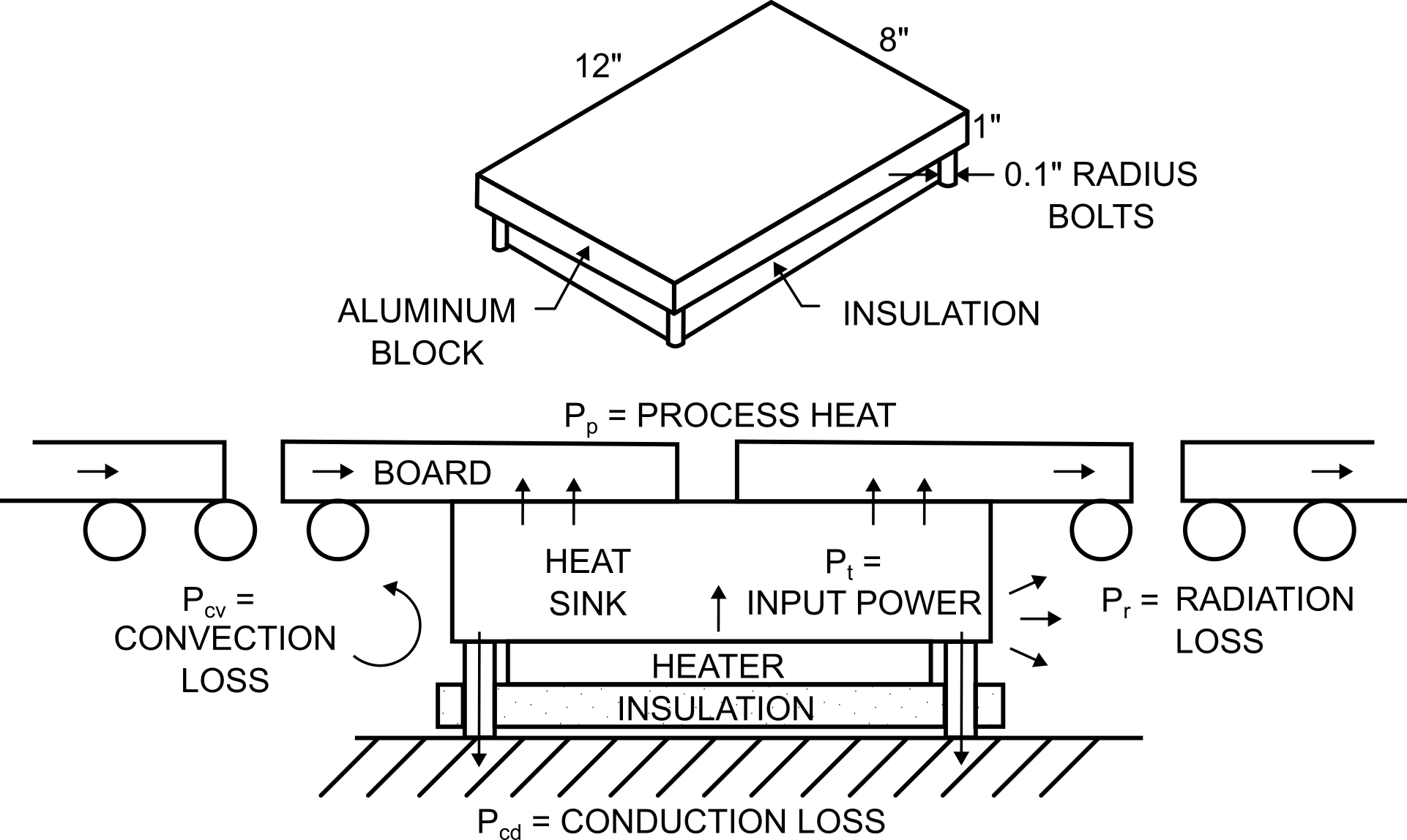
We will estimate the steady-state operating requirements and the warm-up requirements. The estimated minimum wattage required will be the greater of the two sets of requirements, plus a small buffer.
Inputs
Common
Conductive Losses
When speaking of etched-foil heaters, conductive loss generally refers to loss through insulation layers or heat sink mounting hardware. The conductive loss also depends upon the ambient temperature.
Radiation Losses
Radiation is heat emitted as infrared energy. The radiation losses also depend on the ambient temperature and the final temperature of the heat sink.
Natural Convection Losses
Natural convection occurs when heated air rises and creates air currents. The natural convection losses also depend on the ambient temperature and the final temperature of the heat sink.
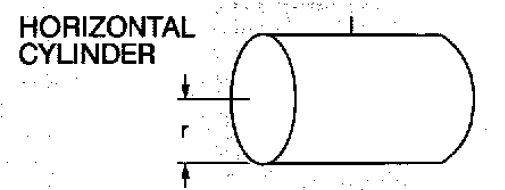
Forced Air Convection Losses
Forced air convection occurs when fans or wind drive air past the heater. The forced air convection losses also depend on the ambient temperature and the final temperature of the heat sink.
Warm-up Heat
Warm-up heat is the heat required to bring the heat sink to temperature in the desired time, plus heat to compensate for conductive, radiant, and convective losses during warm-up.
Process Heat Requirements
Process heat represents work done by the heater to thermally process some material. Examples of process heat are melting a plastic film placed over a heat sink or heating a PCB to a set temperature.
Results
After comparing the warm-up heat and the operating heat, we estimate the minimum heater wattage.
To reach this estimate, we calculate the operating heat.
We compare the operating heat to the warm-up heat.
We add 10% buffer to the greater of the two in order to estimate the minimum heater wattage.